SEO Keywords Targeted
Smart Inventory Scanning for Carriers
In the last mile delivery world, your warehouse is more than just a stop—it’s the launchpad. Every delay, mismatch, or missing item starts (or ends) with poor inventory control. That’s why TrackOps, developed by Mondo Cloud Solutions in London, Ontario, provides a dedicated Inventory Tracking & Scanning module tailored for last mile carriers and white glove delivery providers across Canada and the U.S.
Using Android-based handheld devices, label printers, and real-time syncing via API or Excel, our solution eliminates inventory blind spots, reduces losses, and enhances retailer confidence—especially when working with major brands like Home Depot and Floor & Decor.
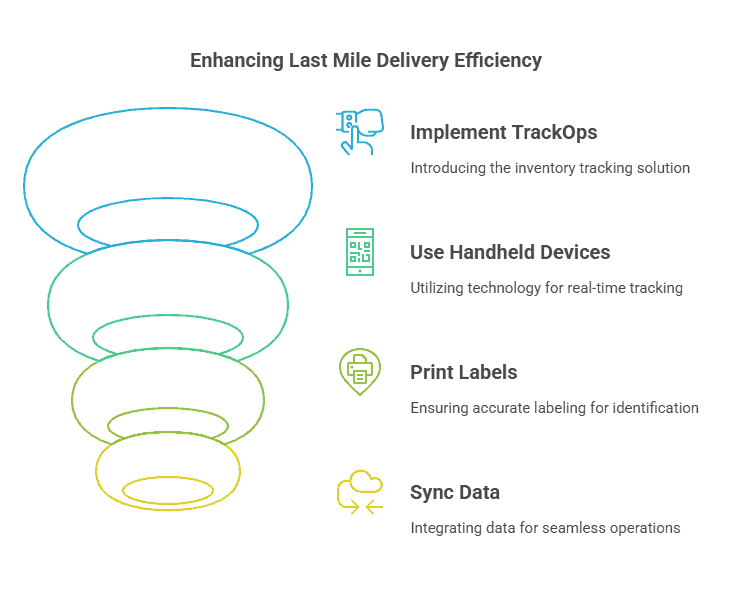
Why Inventory Tracking Is a Game-Changer in Last Mile
Traditional inventory systems don’t account for the unique flow of last mile operations—store pickups, returns, warehouse holds, cross-docking, and serial-tracked products all behave differently.
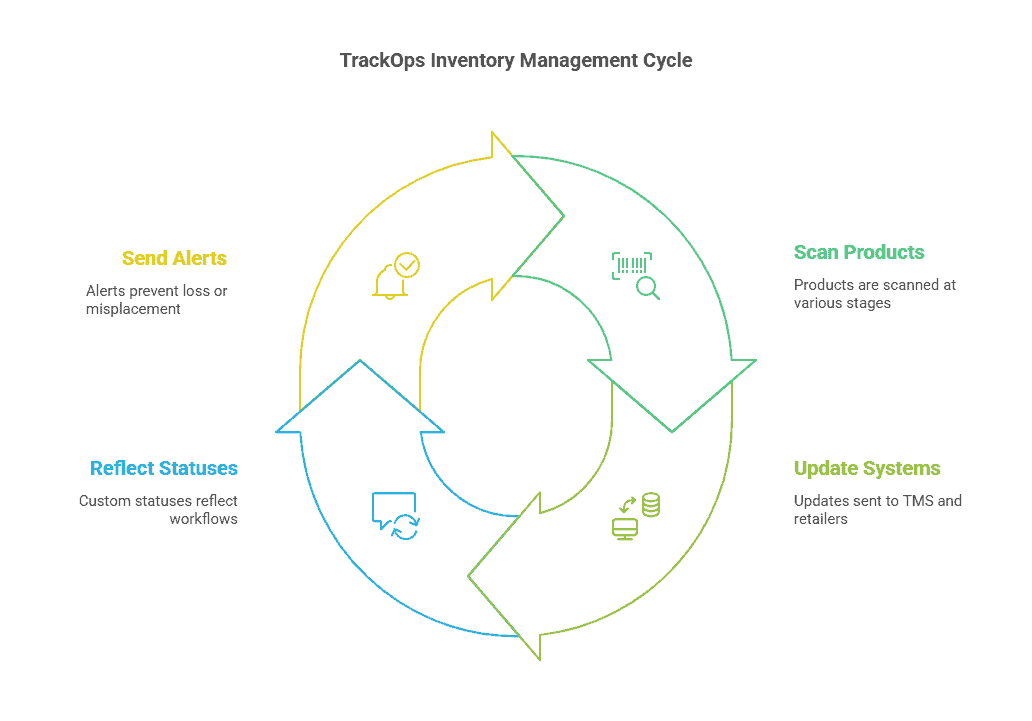
With TrackOps:
Products are scanned on receipt, storage, release, or return
Updates are sent instantly to both TMS systems and retailers
Custom inventory statuses reflect your real-world workflows
Alerts ensure items aren’t forgotten or misplaced
This creates a 360° view of your warehouse operations—accessible, auditable, and automated.
Core Features:
Android-Based Scanning App
TrackOps runs on Android handhelds, allowing staff to scan SKUs, serial numbers, or QR codes. It integrates seamlessly with label printers for instant identification.
Label Printing & Custom Tags
Labels can include:
SKU
Serial number
Retailer logo
Delivery reference
Storage location
Real-Time System Updates
As items are scanned, TrackOps pushes updates to:
Your TMS (DispatchTrack, OnTime360, or custom)
Retailers via API, XML, Excel, or email
Internal dashboards and reports
Custom Inventory Statuses
Use statuses like:
Received
Staged
Ready for Delivery
Delayed
Returned
Damaged You define the flow, we automate it.
Retailer-Agnostic Compatibility
Whether your warehouse services one retailer or ten, TrackOps standardizes the flow. One system, infinite flexibility.
How It Works
Inbound Scanning
Warehouse staff scan products upon delivery from retailer or store.Status Logging & Label Printing
TrackOps assigns a status and prints a custom label for warehouse use.Real-Time Sync
Statuses are pushed to retailer systems and your TMS, notifying all parties instantly.Outbound Scanning
Products are scanned again before dispatch to ensure load accuracy.Alerts & Reports
Notifications are triggered for any delays, returns, or inventory holds.
Deep Integration with Other TrackOps Modules
Inventory Tracking doesn’t work alone—it connects with multiple TrackOps services:
Order Integration: Links scanned products to original delivery orders
TMS Integration: Ensures products are assigned correctly to scheduled routes
Status Updates: Tracks product-level status (e.g., delayed, returned, staged)
Billing Automation: Triggers warehouse storage or handling fees
SKU Management: Records serial numbers, batches, and delivery linkage
Enhance the Experience with Mondo’s Supporting Services:
Network Infrastructure
Ensure strong Wi-Fi and device connectivity across your warehouse or depot.
Office 365 Email Alerts
Auto-email reports or scan logs to warehouse managers and CSR teams.
VoIP Communication
Let scanning staff communicate instantly with dispatchers via wireless headsets.
Web Portal Access
Retailers can log in to see scanned inventory and statuses in real time.
Real-Life Use Case:
A carrier in Southwestern Ontario struggled with lost items and mismatches in deliveries. By using TrackOps’ inventory module:
- Product scanning accuracy rose to 99.2%
- Label printing cut packing errors in half
- Daily inventory sync reduced retailer complaints to near zero
Key Benefits:
✔ Increased scan accuracy
✔ Real-time inventory visibility
✔ Customizable flows per retailer
✔ Reduced returns and losses
✔ Integration with TMS and billing
✔ Instant email or system alerts
Conclusion:
If your delivery operation still relies on pen-and-paper or fragmented tools for inventory, it’s time to upgrade. TrackOps Inventory Tracking & Scanning provides the last mile visibility you need—down to the barcode. For carriers across Canada and the U.S., especially those operating in London, Ontario, TrackOps delivers warehouse efficiency, scanning precision, and retailer peace of mind.
Over 1.3M orders & invoices processed
trusted by 50+ global partners for 12+ years.
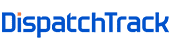
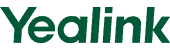

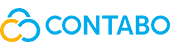
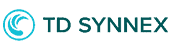
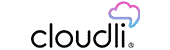
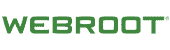
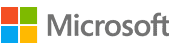